MicroC® vs. Crude Glycerin: Which Carbon Source Reigns Supreme for Biological Nutrient Removal?
| Avoiding process headaches and operational downtime from making the wrong carbon source choice is critical for wastewater treatment plant operators whose time is in short supply.
The Choice is Clear
When it comes to choosing the right carbon source for biological nutrient removal (BNR), not all options are created equal, especially when it comes to making the best choice for glycerin-based carbon sources. In terms of glycerin-based carbon sources BNR plant operators generally have two main choices, EOSi’s MicroC® 2000 and crude glycerin. For reliability, peace of mind and overall cost-effective performance, the choice is clear - MicroC 2000 wins the day.
Manufacturing Quality Makes a Difference
EOSi’s MicroC® 2000 is a refined glycerin-based product, meaning that it has undergone manufacturing processes to remove excess levels of impurities such as salts, methanol, and other residues found in crude glycerin. While crude glycerin may seem like a “cheaper” solution in the short-term, MicroC offers unmatched advantages in product quality, supply chain reliability, and long-term cost savings. Unlike crude glycerin, which can vary in composition and availability, MicroC provides a consistent, higher-quality formula tailored to optimize biological nutrient removal and significantly eliminate quality related issues that lead to downtime.
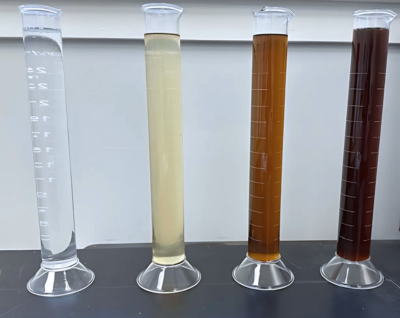
Crude glycerin is a “dirtier” form of the glycerol byproduct stream derived from biodiesel production. While crude glycerin may be a cheap carbon source, it typically is directly shipped from biodiesel manufacturers with no further processing and clean-up steps, which means it often contains unwanted impurities and contaminants grouped under the acronym MONG — material, organic, not-glycerin — fatty substances and solid material that cause problems with wastewater treatment pumps, tanks, handling equipment, and treatment processes. Avoiding clogged feed lines and pump system failures due to poor quality is the single most cited reason plant operators make the switch to MicroC 2000 which has little to no MONG content.
| Right: Crude glycerin samples tested by EOSi lab indicate a range in characteristics and quality.
Spotty quality control and chemical inconsistency of crude glycerin also wreaks havoc with optimizing carbon source feed rates within treatment systems with little tolerance for chemical variability. Guaranteeing product consistency is the primary reason why EOSi maintains in-house testing labs at every MicroC manufacturing location and is dedicated to frequent sampling and testing at every step of the production and delivery fulfillment process. EOSi’s extensive quality process ensures that plant operators get the same quality with every delivery.
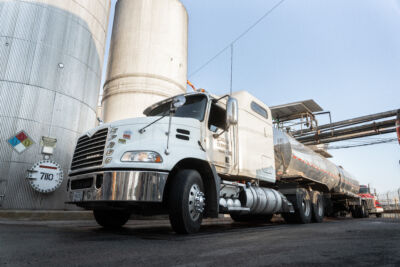
Supply Chain Support Produces Better Outcomes
EOSi is dedicated to manufacturing MicroC® 2000 for BNR, supported by a robust supply chain network of over 20 sites across North America, reliable transportation and an operations team committed to ensuring tanks never run dry.
Alternatively, crude glycerin is often supplied directly from a single source biodiesel manufacturer whose primary focus is fuel production, not wastewater treatment. Unlike EOSi, these suppliers do not specialize in BNR applications. As a result, if plant operations are disrupted or additional support is required, the necessary expertise is not available to ensure things go right.
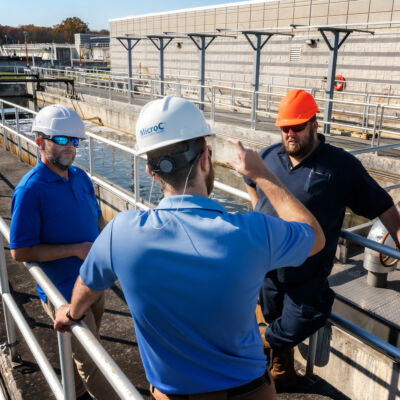
MicroC® 2000 Advantage: Expert Insight & Automation
MicroC® is backed by EOSi’s expert in-house technical support and cutting-edge Nitrack® automation which helps wastewater treatment facilities streamline operations, reduce feed rate costs, and enhance system performance—ensuring efficiency and compliance without the risks of variability.
Most operators express the real differentiating value between crude glycerin and MicroC is the expertise, experience, and immediate availability of EOSi’s process engineers dedicated to helping customers use MicroC most cost-effectively. Additionally, EOSi’s Nitrack automated dosing control system helps boost efficiencies and reduce MicroC feed costs by up to 30% by analyzing fluctuations in influent loading, accurately predicting the precise chemical dosing, and minimizing unnecessary dosing by dynamically optimizing the feed rate.
EOSi is the only company on the market that provides the combination of non-hazardous glycerin-based carbon sources, a proven automation control system that optimizes the feed rate, and the engineering support to back it up year-round. Facilities who initially favored crude glycerin due to lower cost discovered that poor quality crude glycerin did not permit their biological nutrient removal process to operate properly and they often switched back to MicroC in as little as three months and never switched again.